Meet the Author
Chinaland Solar Energy Co., Ltd. (SUNERGY)
Established in 2008, Chinaland Solar Energy Co., Ltd. (SUNERGY) stands as a beacon of innovation and excellence in the realm of solar energy. As a high-tech enterprise, SUNERGY is dedicated to the comprehensive advancement of solar technology, spanning research and development, production, sales, and service of solar modules and photovoltaic power generation systems.
With a steadfast commitment to quality and sustainability, SUNERGY has emerged as a leading brand in the photovoltaic industry. Our reputation for excellence is built upon a foundation of industry-leading module R&D capabilities and manufacturing levels, ensuring that every product deliver is of the highest standard.
As advocates for a greener, more sustainable future, the experts at SUNERGY are passionate about empowering individuals and communities to harness the power of the sun. Through their expertise and dedication, they continue to pave the way for a brighter tomorrow, one solar panel at a time.
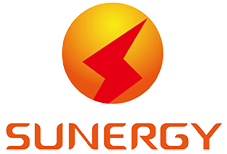
Solar panels are pivotal in the global shift towards renewable energy, converting sunlight into electricity. As demand for clean energy grows, understanding the intricate process of solar panel manufacturing becomes essential. This article provides a detailed exploration of how solar panels are made, from raw materials to finished products, highlighting each significant step in the process.
Step 1: Raw Materials
Silicon: The Heart of Solar Technology
Silicon is the cornerstone of most solar cells, derived primarily from silica found abundantly in sand. Its excellent semiconductor properties make it ideal for photovoltaic (PV) technology.
Extraction & Purification Process
Quartz Mining: Silica is extracted through mining methods, usually involving open-pit or underground techniques.
Smelting: The silica is subjected to high temperatures (around 1,500°C) in an electric arc furnace, where it combines with carbon to produce metallurgical-grade silicon.
Chemical Treatment: To achieve the purity needed for solar applications, metallurgical-grade silicon undergoes further purification. In the Siemens process, it is converted into trichlorosilane gas and then distilled. The purified gas is then reduced back into high-purity polycrystalline silicon through thermal decomposition.
Other Essential Materials
Besides silicon, several other materials contribute to the functionality and durability of solar panels:
Metals:
Silver: Used for electrical contacts due to its superior conductivity. It is typically printed onto the cells in fine lines using screen printing techniques.
Aluminum: Commonly utilized for framing because it is lightweight, corrosion-resistant, and cost-effective.
Glass:
High-transparency, low-iron tempered glass protects solar cells while allowing maximum sunlight penetration. This glass is designed to withstand harsh environmental conditions, including hail and wind.
Encapsulation Materials:
Ethylene-Vinyl Acetate (EVA): This polymer is used to encapsulate the solar cells, providing insulation and protection against moisture and mechanical stress.
Backsheet:
Usually made of durable polymers, the backsheet protects the solar cells from environmental factors and provides electrical insulation.
Step 2: Silicon Purification
Purifying silicon is vital as it directly impacts the efficiency of the final solar panels. The purification process includes:
Quartz Mining: Extracting silica from the earth, often through large-scale mining operations.
High-Temperature Reduction: The smelting phase involves mixing silica with carbon at extremely high temperatures, resulting in metallurgical-grade silicon.
Further Refinement: Through chemical reactions, metallurgical-grade silicon is transformed into trichlorosilane gas, which is then purified and thermally decomposed to yield high-purity silicon suitable for solar cell production.
Step 3: Wafer Production
The silicon obtained is cast into large ingots, which are then sliced into wafers. The wafer production process involves:
Czochralski Process
This technique produces single-crystal silicon ingots. A seed crystal is dipped into liquid molten silicon and slowly withdrawn, forming a large cylindrical ingot.
Slicing
Once cooled, the silicon ingots are sliced into thin wafers, typically around 180 to 200 micrometers thick. Slicing is performed using wire saws that minimize material loss and ensure uniform thickness.
Polishing
To enhance the quality of the wafers, they may undergo a polishing process to eliminate surface defects and prepare them for further processing.
Step 4 : Cell Fabrication
Transforming silicon wafers into functional solar cells involves several critical steps:
Doping
Doping introduces impurities into the silicon to create the p-n junction essential for solar cell operation. Phosphorus is introduced to form n-type silicon, while boron is used to create p-type silicon. The interface between these two types generates an electric field, allowing for the flow of electrons when sunlight hits the cell.
Texturization
The surface of the silicon wafers is textured to increase light absorption. Techniques such as wet chemical etching create microscopic structures that trap light, minimizing reflection and maximizing sunlight captured by the cell.
Anti-reflective Coating
An anti-reflective layer, typically made of silicon nitride, is applied to the surface of the wafer. This coating reduces reflective losses and improves the overall efficiency of the solar cell by ensuring that as much light as possible enters the silicon.
Metal Contacts
Metallic contacts are added to the solar cells to allow the collection and transport of generated electrons. Silver paste is screen-printed onto the front side, forming fine grid-like patterns to minimize shading while ensuring efficient conduction. Aluminum is typically used for the rear contact.
Step 5 : Module Assembly
After the solar cells are fabricated, they are assembled into modules:
Cell Interconnection: Individual solar cells are connected in series and parallel configurations to form a solar module.
Encapsulation: Cells are sandwiched between layers of EVA and covered with a protective glass layer.
Framing: An aluminum frame is added to provide structural support and facilitate installation.
Testing: Modules undergo rigorous testing to ensure performance and quality standards before being packaged for shipment.
Step 6 : Installation and Integration
Once manufactured, solar panels are shipped to distributors, installers, or directly to consumers. The final step involves integrating the solar panels into a solar energy system, including:
Mounting: Fixing panels onto rooftops or ground-mounted systems.
Electrical Connections: Connecting panels to inverters, batteries, and the electrical grid.
Conclusion
The manufacturing of solar panels is a complex process that transforms raw materials into a crucial technology for sustainable energy production. As demand for clean energy continues to grow, advancements in solar technology aim to improve efficiency, reduce costs, and make solar energy accessible to a broader audience. Understanding how solar panels are made highlights their importance in the transition to a greener future.